
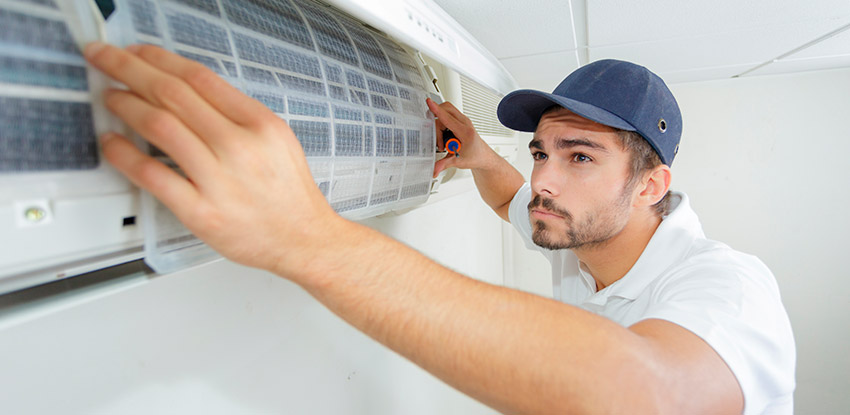
In hot forging processes, the surface properties are strongly affected by the growth of oxide scale, which influences the material flow, friction, and product quality of the finished component. In order to accurately model hot forging processes with finite, element-based numerical methods, reliable models are required, which take the material behaviour, surface phenomena of die and workpiece, and machine kinematics into account. Increasing product requirements have made numerical simulation into a vital tool for the time- and cost-efficient process design. After presenting the necessary adaptive remeshing steps, some 3D analytic and numerical results using the proposed adaptive strategy are given to demonstrate the capabilities of the proposed equilibrated approach and to illustrate some practical characteristics of our remeshing process. A special attention is given to restore the local mechanical equilibrium of the system with a new methodology. Therefore, several transfer techniques are described and compared. Once a new mesh is generated, all history-dependent variables must be carefully transferred between subsequent meshes. The main idea is to use the h-type adaptive mesh in combination with an a-posteriori error estimator measured (by the energy norm) on each finite elements to locally control the mesh modification-as-needed.

In this work, a fully automated adaptive remeshing strategy, based on a tetrahedral element for 3D metal forming processes, was proposed in order to solve problems associated with the severe mesh distortion that occurs during the computation. In addition, the ALE approach accuracy for thermomechanical modeling was verified. It was concluded that some areas in both paths might be considered as approximately under pure compression stress state. Two paths were defined to study the stress state inside the sample, in the radial direction (equator line) and axial direction (axial line). The results from both models are in good agreement between them and agree with the force vs.
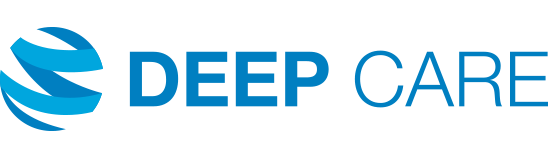
The Lagrangian model was done in QForm, and the ALE model was done in LS-Dyna. However, it is not possible to achieve ideal conditions in actual experiments. Ideally, under pure compression, these parameters' values are − 1/3 and − 1, respectively. The stress state is evaluated through the triaxiality factor and Lode parameter. After that, a study on the material's stress state evolution inside the specimen is provided. This comparison aims to verify the ALE's approach suitability for modeling thermomechanical processes. In this study, a comparison between the well-established Lagrangian approach and the Arbitrary Lagrangian–Eulerian (ALE) approach is presented.
